Control valves play a pivotal role in modern industrial processes. They ensure the accurate regulation of fluid flow, pressure, and temperature. These devices are fundamental for the safe and efficient operation of systems in various industries.
In this article, we will explore what a control valve is, its key components, and its significance. We will also discuss the control valve symbol, the control valve diagram, and the control valve assembly.
What Is A Control Valve?
A control valve is a mechanical device used to regulate the flow and pressure of fluids in a pipeline or process system. Examples of these are liquids, gases, or slurries.
A control valve functions by adjusting the size of the flow passage, thereby controlling how much fluid can pass through. This enables the system to maintain specific operating conditions like desired pressure or temperature.
Control valves are a critical component of process control systems. They receive signals from controllers to adjust their settings and maintain optimal operating parameters. These signals can be pneumatic, electrical, or hydraulic, depending on the system’s design.
Control Valve Symbol
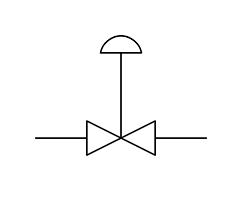
In process engineering, visual symbols are used to represent control valves on system diagrams. The control valve symbol usually consists of a valve body depicted by a square or a rectangle, with lines indicating the connection to pipelines.
These symbols are standardized to ensure universal understanding across industries. For instance, a globe valve might appear as a circle with two intersecting lines in the diagram. Other types of control valves, like ball or butterfly valves, have distinct variations of this symbol. This helps engineers and operators quickly identify their function and placement in the system.
Control Valve Diagram
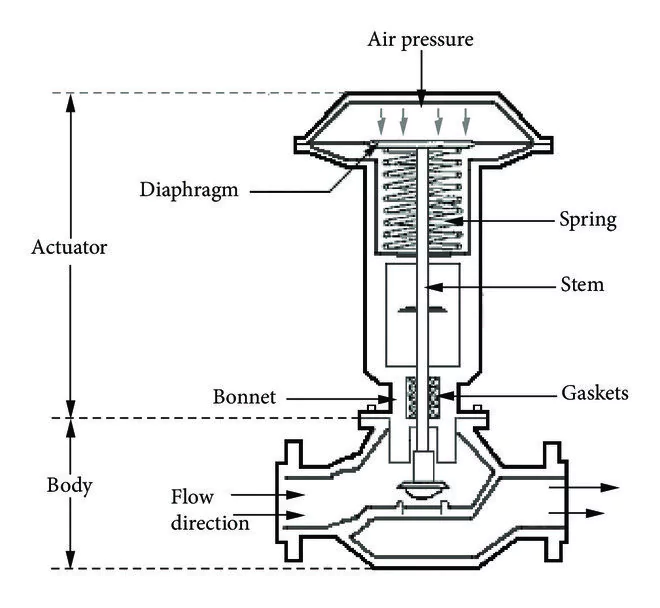
A control valve diagram provides a detailed illustration of the valve’s components and how they interact to regulate flow. It typically shows:
- Valve Body: The main housing that contains the internal components.
- Actuator: A device (pneumatic, electric, or hydraulic) that moves the valve mechanism.
- Positioner: Ensures the valve reaches the precise position needed to regulate flow as per the control signal.
- Flow Path: Demonstrates how the fluid enters and exits the valve.
This diagram is an essential tool for engineers to understand the operational flow, troubleshoot potential issues, and ensure proper maintenance.
Control Valve Assembly
The control valve assembly refers to the complete set of components that make up the control valve system. This assembly ensures the valve’s seamless operation in various industrial settings. It includes:
- Valve Body: Houses the internal parts and determines the flow characteristics.
- Trim: Internal components like the plug, seat, and stem that directly affect flow control.
- Actuator: Provides the necessary force to move the valve’s trim.
- Positioner: Enhances the precision of the actuator, ensuring the valve opens or closes accurately.
- Accessories: Components such as solenoid valves, limit switches, and handwheels that support functionality and manual operation.
The design and assembly of these components determine the valve’s suitability for specific applications.
Applications of Control Valves
Control valves are vital in numerous industries, including:
- Oil and Gas: Regulating crude oil flow, refining processes, and pipeline pressure.
- Chemical Processing: Ensuring precise mixing, pressure control, and reaction conditions.
- Power Plants: Managing steam flow to turbines and cooling systems.
- Water Treatment: Controlling flow rates in filtration, desalination, and distribution systems.
- Metallurgy: Regulating molten metal flow in production and cooling systems.
By enabling fine-tuned control of processes, control valves contribute to increased efficiency, safety, and cost-effectiveness.
How to Choose the Right Control Valve
Selecting the appropriate control valve involves several considerations:
- Process Requirements: Understand the fluid type, pressure, and temperature range.
- Valve Type: Choose from options like globe, ball, butterfly, or plug valves based on application needs.
- Material Compatibility: Ensure the valve materials are resistant to the fluid being handled, especially in corrosive environments.
- Control Precision: Evaluate the valve’s ability to respond accurately to control signals.
- Manufacturer Expertise: Opt for trusted manufacturers like Gowin, known for delivering quality products and services.
Why Choose Gowin for Your Valve Needs?
When it comes to control valves, quality and reliability are paramount—and that’s where Gowin excels. With over 16 years of industry expertise, Gowin has established itself as a trusted partner to leading global industries. These would include oil and gas, chemical processing, power generation, metallurgy, and water supply systems.
What Sets Gowin Apart?
- Unwavering Quality Standards
Gowin is proudly ISO-certified (ISO9001 & ISO14001) and holds industry-recognized certifications such as API6D, TS, OHSAS45001, Fire Safety API607, and API6FA.
- Global Reputation for Excellence
From local projects to international collaborations, Gowin is known for delivering valves that exceed expectations.
- Tailored Solutions for Unique Needs
Every industrial process is different, and Gowin recognizes the need for customized solutions.
References
Journal of Control Science and Engineering; Chao Lu and Zhao Dong; 2023 (https://www.researchgate.net/journal/Journal-of-Control-Science-and-Engineering-1687-5257)
Gas Well Deliqualification; James F. Lea Jr and Lynn Rowlan; 2019 (https://www.sciencedirect.com/topics/earth-and-planetary-sciences/automatic-control-valves)