Industrial valves play a crucial role in polysilicon production, specifically in managing the proper flow of hazardous and corrosive chemicals throughout every manufacturing phase. Thus, they should be strong, reliable, efficient, safe, and of high-quality.
Learn about industrial valves and polysilicon materials in this guide that will also tackle:
– Properties and uses of polysilicon material
– Challenges and requirements in polysilicon production
– How to choose the right industrial valve
What is Polysilicon?
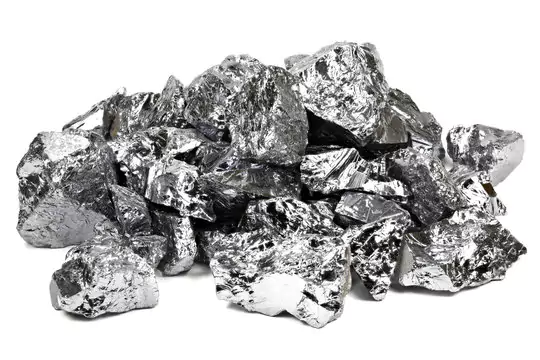
Polysilicon, whose complete term is polycrystalline silicon, refers to a purified version of silicon consisting of p-type and n-type components. This material is made up of several tiny silicon crystals that have been extracted from quartzite, a type of rock known for its high crystalline properties and nature, hence its name.
Polysilicon Material: Properties and Uses
The properties of the polysilicon material are:
- High purity: Polysilicon materials are known for their many properties, including being a high pure form of silicon typically around 99.99994995 percent pure on average. This means the material is highly refined.
- Electrical conductivity: This property of the material makes its conductivity controllable, which is why it is efficient for applications that include gate electrode material, conductor or resistor, ohmic contact, thin film, and solar cells, among many other industrial uses.
- Thermal resistance: The resistance properties of this material are also unmatched, such as how it holds out against thermal elements. This is crucial for its applications in electronics and solar energy.
- Corrosion resistance: Generally, polysilicon is resistant to several corrosive environments, particularly unlike other materials for applications like solar energy and microelectronics.
The most common applications of polysilicon are:
Solar Panels
It is remarkable for its use in making solar panels because of its high purity properties, as well as electrical conductivity. Polysilicon’s qualities are ideal for making solar cells and digital devices, such as, but not limited to smartphones, transistors, vehicle electronics, diodes, and integrated circuits.
Semiconductors
This material is also touted as a very important feedstock not only for solar cells, but also for semiconductors, which constitute semiconductor-based devices such as diodes, transistors, and integrated circuits, too. Furthermore, the microchips found inside your favorite devices are also made with polysilicon.
Other Applications
Polysilicon is also used in the aerospace and automotive industries, photonic devices, thin-film transistors, micro-electromechanical systems or MEMS, and photovoltaic modules.
Polysilicon Production: The Challenges and Industrial Valve Requirements
A chemical procedure known as Siemens is responsible for producing this material. This process involves silicon deposition usually from trichlorosilane (SiHCl3), a gaseous compound consisting of silicon, onto high-purity rods of silicon. Therefore, considering those, the process necessitates extreme care when managing challenges, such as what you’ll learn next.
These challenges are:
- High temperatures: For you to be able to produce the best polysilicon materials, there must be intense temperatures, usually around up to 1,150 degrees Celsius. However, without proper management, issues like energy inefficiency, equipment wear, and potential contamination may occur, affecting quality.
- High pressures: Since the production process requires high pressure, the equipment’s integrity may suffer if left unaccounted for, as well as the increased chances of gas leaks. When these happen, the processes get complicated, leading to lower output and higher operational expenditures.
- Purity control: Aside from the highly automated systems for monitoring and control, meticulous refining processes are also a prerequisite to achieve solar-grade silicon, but contamination and environmental factors may impact quality as well.
In order to combat those challenges above, industrial valves are used. But for them to be efficient, there are requirements.
- Material durability: Polysilicon production is a demanding feat, with you encountering high temperatures and abrasive materials. Thus, top-notch valves are needed for the process to run smoothly.
- Valve design features: The best industrial valves for polysilicon production should carry these important features, such as materials and coatings, stem design, seating, and packing. The valve design must also be clean and organized.
6 Types of Industrial Valves Used in Polysilicon Production
There are six significant types of industrial valves used in polysilicon production:
Valve Type | Function | Application |
Industrial Ball Valve | On-off control, isolates production line sections | Used for isolation during maintenance and emergency shutdowns |
Industrial Control Valve | Manages hazardous chemical flow under high pressure | Controls chemical flow in high-pressure environments |
Industrial Check Valve | Prevents gas or liquid backflow, protects system from contamination | Prevents backflow and contamination |
Industrial Pressure Relief Valve | Releases excess pressure automatically to protect equipment | Prevents equipment damage from overpressure |
Industrial Globe Valve | Provides precise flow control for liquids and gases | Adjusts flow rates and chemical concentrations |
Industrial Needle Valve | Ensures precise control of corrosive liquids and gases under high pressure | Regulates flow in high-pressure and high-temperature environments |
1. Industrial Ball Valve
These valves stand out for their durability and capability to provide tight seals, so they are best for the on-and-off control phases of the production. They won’t fail you when isolating parts of the production line is needed amidst maintenance and emergency shutdowns.
2. Industrial Control Valves
These essential valves take charge of hazardous chemical flow management, or managing against trichlorosilane chemicals under high pressure. They can withstand leakage, improve safety, and maintain process efficiency, allowing you to produce only the highest-quality materials.
3. Industrial Check Valves
Meanwhile, these valves are responsible for safeguarding the production process from gas or liquid backflow, for once these occur, contamination takes place.
4. Industrial Pressure Relief Valves
Overpressure can take its toll upon production, and to protect your equipment from this, pressure relief valves are installed in critical parts of the system. As their name implies, they release pressure automatically when a certain threshold is reached, ensuring the overall safety of your production.
5. Industrial Globe Valves
The function of these globe valves is for precise flow control when distributing liquids and gases. They can finely adjust and customize flow rates, which is ideal for maintaining the needed flow dynamics and chemical concentrations throughout the process.
6. Industrial Needle Valves
Last but not the least are industrial needle valves. They are used to ensure the flow control of corrosive liquids and gases is as precise as possible. Their design prevents leakage and guarantees the most accurate regulation, enhancing efficiency and safety in environments with high pressures and temperatures.
8 Considerations for Choosing an Industrial Valve for Polysilicon Production
Using valves for polysilicon production is crucial, but how do you choose the most appropriate for your needs? Consider the following:
Consideration | Description |
Temperature Resistance | Valve must withstand high temperatures without failure. |
Pressure Resistance | Ensures the valve can handle high pressure without leaks. |
Corrosion Resistance | Protects against harsh chemicals, improving durability. |
Flow Control and Precision | Allows accurate regulation of production processes. |
Valve Size and Capacity | Proper size ensures efficient material flow and scalability. |
Seal Integrity and Durability | Prevents leaks and ensures long-term reliability. |
Safety and Compliance | Must meet safety standards and ensure worker safety. |
1. Temperature Resistance
The best industrial valves are those with the highest resistance against temperature as they must be able to withstand intense heat across the production process, thereby maintaining efficiency, and keeping material degradation and failure at bay.
2. Pressure Resistance
Since the production usually occurs under high pressure, resistance against it is important. This ensures leaks won’t happen, maintaining safety and guaranteeing consistent performance.
3. Corrosion Resistance
On the other hand, this ensures your valves can be protected against harsh chemicals during production, enhancing durability, cutting down on maintenance costs, and preventing operational mishaps.
4. Flow Control and Precision
At the same time, your valves must be able to provide unparalleled flow control and precision. These ensure your valves can accurately regulate the production processes, optimize efficiency, maintain consistency, and prevent waste.
5. Valve Size and Capacity
The size and capacity of the valve must never be set aside. The right sizing and hold ensures efficient material flow, supporting scalability and minimizing bottlenecks.
6. Seal Integrity and Durability
These prevent leaks in your valves, guaranteeing they are reliable, safe, and protected from the harsh conditions of the process.
7. Safety and Compliance Standards
Of course, your industrial valves must be safe to use from square one to the last phase, as well as must comply with standards to ensure the safety of the procedure and of the workers.
Conclusion
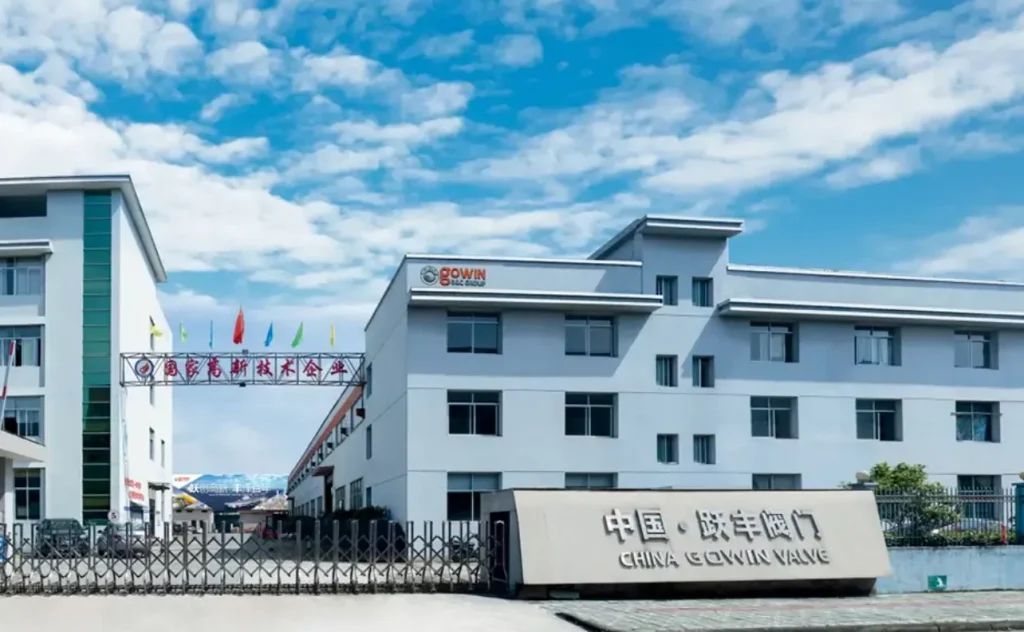
Being a highly efficient material, polysilicon is produced under meticulous processes. Without the use of industrial valves, you are sacrificing multiple aspects, from the quality of your products to the safety of those in the workplace.
Seek out some of today’s best industrial valves from Gowin, which has consistently been delivering top-tier valve products – ball, gate, globe, check valves, and more – to industries such as gas, oil, water, metallurgy, chemical, and energy for almost two decades now. You can connect with them via email, phone, or their social media accounts.